Кайдзен — японский подход к управлению бизнесом или другими проектами, который предполагает непрерывные улучшения. Термин появился сравнительно недавно, в 1986 году. Но некоторые методы и инструменты кайдзен известны с начала XX века.
Разобрались, из чего состоит кайдзен и какой эффект может принести применение подхода на производстве.
Научные разработки, которые легли в основу кайдзен
Научная организация труда в СССР в 1920–1930 годы
Идейными вдохновителями современных управленческих подходов можно смело называть советских учёных. В 1921 году был создан Центральный институт труда, который занимался научной организацией труда — НОТ. Одним из его основателей стал Алексей Капитонович Гастев, его главный труд называется «Как надо работать». Учёный спорил в переписке с создателем конвейера Генри Фордом. Идеи Гастева звучат современно:
- человеческий фактор является на производстве одним из главных;
- необходимо повышать культуру советских рабочих;
- у каждого действия есть оптимальная техника движений, позволяющая эффективно использовать силу;
- каждый станок должен быть превращён в научно-исследовательскую лабораторию по поиску новых решений.
В 30-е годы в Японии был даже создан институт по изучению советских наработок. В 1938 году Гастев был арестован и через год расстрелян, по некоторым данным как раз из-за связей с Японией.
Реформа управления Toyota в 1950-е годы
После Второй мировой войны японские компании искали способ быстрого восстановления. Пионером стала Toyota Motor Corporation.
В основе Toyota Production System лежат два принципа:
- Just-in-time, JIT, по-русски «точно-в-срок», ТВС. На линиях производится ровно столько автомобилей, сколько нужно покупателю, это избавляет, с одной стороны, от накопления запасов на складах, с другой — от простоев из-за нехватки материалов.
- Jidoka, по-русски «дзидока», — автоматическая система контроля качества. Когда где-то происходит сбой, система немедленно сигнализирует, ошибку исправляют или забракованную деталь убирают с производственной линии. Это позволяет сократить количество дефектных изделий на выходе.
Концепция Lean production, бережливого производства, в 1980–1990 годы
После того, как японские автомобили начали превосходить по качеству американские, на Западе заинтересовались восточными технологиями в управлении труда. Концепция бережливого производства возникла в США в результате переосмысления и заимствования японских идей.
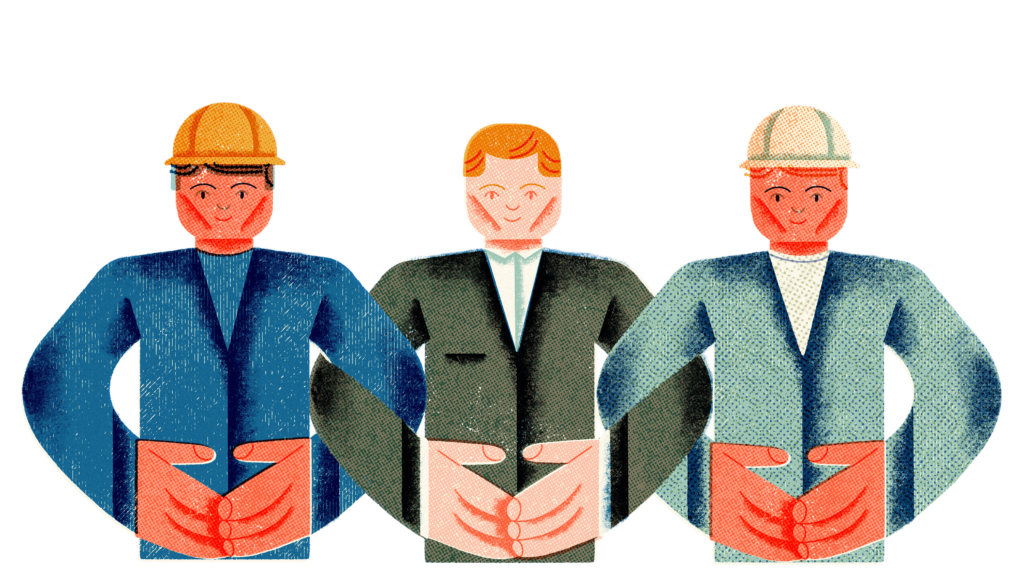
Принципы кайдзен
Создатель кайдзен Масааки Имаи ездил в США в составе японских деловых делегаций по обмену управленческим опытом. В итоге он презентовал собственную концепцию организации труда, которая вместила накопленный опыт.
По мнению Масааки Имаи, кайдзен — это не просто непрерывное совершенствование. К этой формуле надо добавить компоненты every day, everybody, everywhere — каждый день, каждый сотрудник, каждое подразделение компании. Изменения должны начинаться с топ-менеджмента. Бесполезно внедрять кайдзен среди рабочих, не охватив управленческий аппарат, бухгалтерию, отдел кадров.
Как и в бережливом производстве, нужно ориентироваться на потребителя — внутреннего или внешнего. Вот что затягивает производство и делает его неэффективным:
- перепроизводство — выпуск большего количества продукции, чем нужно потребителю;
- простои — например, из-за того, что поставки сырья запаздывают, или из-за пересменки;
- транспортировка между цехами или отделами;
- излишняя обработка, которая возникает из-за некачественных инструментов или усложнённых технологий;
- создание запасов на складах, которые никому не нужны и устаревают;
- лишние движения, которые заставляют рабочих расходовать энергии больше, чем нужно;
- дефекты и брак.
Для реализации этих элементов важны несколько компонентов.
Командная работа. Это основа всех процессов кайдзен. Работа в команде взаимно обогащает людей. Сотрудники должны делать как можно больше для блага коллег, выполнять работу в срок, учиться новому друг у друга.
Личная дисциплина. Каждый сотрудник должен уметь управлять своим временем, качеством работ, соблюдать требования и регламенты, осмысленно расходовать материальные и финансовые ресурсы.
Высокий моральный дух. Чтобы сохранить его, руководство может внедрять разные поощрения — создавать хорошие условия труда, выплачивать пособия, предоставлять кредиты на льготных условиях и так далее.
Группы мозгового штурма. Необходимо собирать «кружки качества», где люди смогут искать решение проблем и высказывать идеи.
Банк идей по улучшению. Надо дать возможность всем работникам выдвигать идеи и рассматривать их все, какими бы абсурдными они ни казались.
Кайдзен не предлагает революционных решений. В основе прогресса должны быть маленькие шаги: небольшие, но регулярные изменения к лучшему.
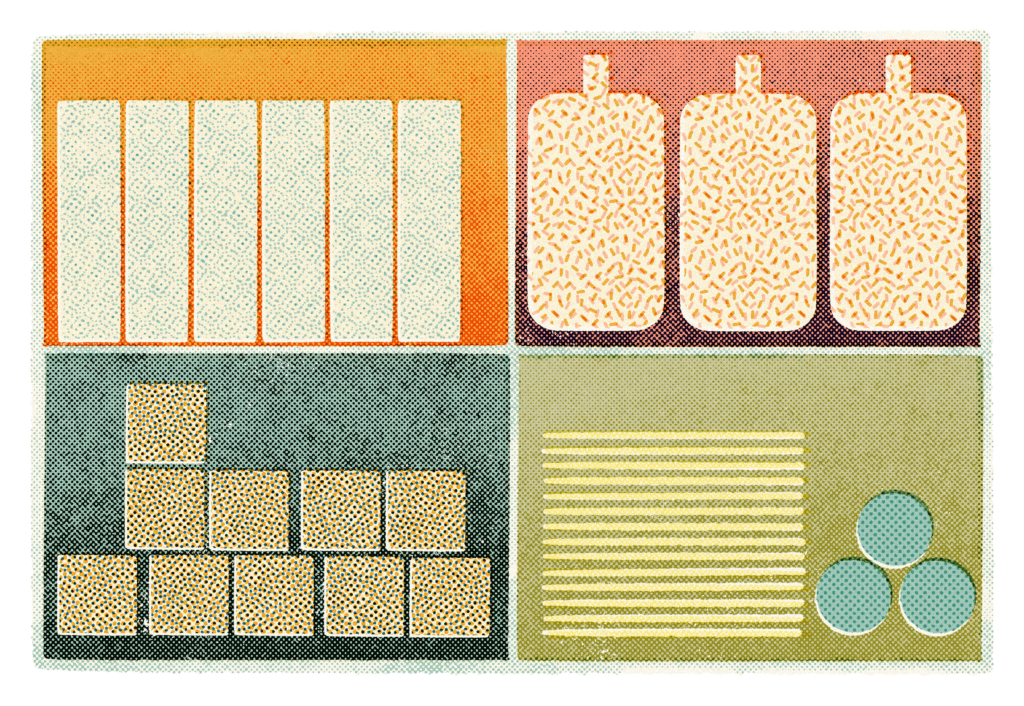
Методы и инструменты
Кайдзен внедряется в виде мероприятий — создания и работы команд, которые решают разные задачи. Они могут функционировать несколько часов, несколько дней или постоянно. Все команды можно разделить на пять групп:
- постоянные — это команды сотрудников, которые решают повседневные задачи;
- по решению проблем — создаются для поиска решения конкретных проблем;
- кросс-функциональные — следят за взаимодействием, оценивают процессы, ищут пути улучшения;
- по реализации решений — создаются из участников трёх предыдущих групп, чтобы внедрять найденные улучшения;
- малые — создаются для решения специфических проблем или внедрения новых решений.
Есть ещё «люди кайдзен» — производственники с большим стажем, которых освобождают от работы, чтобы они ходили по предприятию и искали, что можно улучшить.
Все группы, за исключением постоянных, собираются на так называемых кайдзен-сессиях, или кайдзен-блицах, которые продолжаются от двух до пяти дней. Результатом должна стать выработка новых решений, направленных на улучшение производства.
Метод 5S
В кайдзен важно правильно организовать рабочее место (Масааки называет его Gemba — буквально «место, где происходит работа»).
Метод быстрой переналадки — Single-Minute Exchange of Dies (SMED)
Его разработал инженер Toyota Сигео Синго. По его мнению, процессы переналадки можно разделить на две группы: внутренние, когда нужно останавливать оборудование, и внешние — это подбор деталей и подготовка, которые можно производить без остановки оборудования. Синго утверждал, что переналадку можно произвести в одно касание, сократив издержки.
В рамках концепции кайдзен можно использовать множество других инструментов.
Как элементы кайдзен используют в российских компаниях
В России стратегии на основе кайдзен и бережливого производства постепенно приобретают популярность и внедряются не только на крупных предприятиях. Подход опробовали в торговле и медицине. Но пионерами стали именно производственники.
Алроса. На предприятиях компании успешно внедряют несколько новшеств:
- Метод 6С — создание удобных и безопасных рабочих мест. Первый этап на участках техобслуживания и ремонтов четырёх ГОКов завершился в 2020 году.
- «Фабрика идей» — сбор предложений от сотрудников. За внедрённую идею дают премию. Количество предложений на одного сотрудника не ограничено. Например, слесарь-ремонтник одного из ГОКов предложил 30 идей. За каждую получил премию, и большая часть уже реализована.
- «Идеальная смена» — уход от простоев техники. Чтобы самосвалы и экскаваторы не простаивали во время обеденного перерыва, появились сменные водители — hot seat. Оперативное техническое обслуживание проводится прямо на карьерах.
- Стандартная операционная процедура — СОП. Написали руководства по конкретным ремонтным действиям, снабдили схемами и картинками, привели примеры, как правильно делать и как неверно. Когда каждый делает ремонт по-своему, это может привести к аварийной ситуации.
Мечел. Пилотным объектом на Челябинском металлургическом комбинате стал участок машины непрерывного литья заготовки № 5 в кислородно-конвертерном цехе. Там внедряют:
- Систему 5С для организации рабочих мест — провели аудит.
- Анализ работы оборудования, чтобы заставить его выйти на полную мощь. Обследовали машину непрерывного литья заготовки, составили дорожную карту, сделали графическое представление производственных этапов.
- Стенды для эффективного обмена информацией для сотрудников — разместили их на участке.
После успеха эксперимента решено внедрять технологии в других цехах.
Уральская сталь. На предприятии всерьёз взялись за реорганизацию рабочих мест по методу 5S — решили применить к листопрокатному цеху. В течение трёх лет провели мероприятия:
- Навели порядок в хранении инструментов и материалов, убрали то, что лежит «на всякий случай».
- Места хранения сопроводили информацией, вплоть до фотографий ответственных работников, установили дополнительное освещение, сделали разметку безопасных зон и дорожек, развесили знаки, предупреждающие об опасности.
- Ввели график уборки, теперь в цехе можно встретить даже человека с пылесосом, который собирает промышленную пыль — чтобы люди ей не дышали. На некоторых участках установили контейнеры для раздельного сбора мусора.
- На этапе стандартизации сделали единые шкафчики, причём изготовил их соседний цех металлоконструкций.
Деньги на эти работы появились благодаря «Фабрике идей» — по условиям программы 5% экономического эффекта от рационализаторских предложений возвращаются в родной цех. По словам работников, перемены на производстве не только повышают настроение и производительность труда, но и снижают травматизм, а значит, и издержки.
Данная статья носит не рекламный, а информационный характер. Существуют противопоказания к применению и использованию препаратов и медицинских процедур, которые фигурируют в тексте. Необходимо ознакомиться с инструкцией по применению препаратов и процедур и получить консультации специалистов.